Limit samples are essential in manufacturing
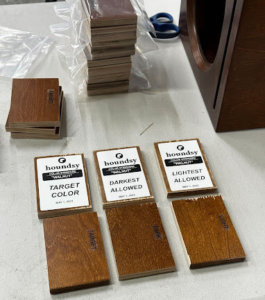
Acceptable dark, light, and mid limit samples for the Houndsy Kibble Dispenser.
As anyone who’s worked in hardware will tell you: Manufacturing the same thing over and over is hard. In an ideal world, each part is manufactured exactly to specification and looks immaculate. In reality, each and every part deviates from the ideal shape and appearance by some amount due to subtle inconsistencies in manufacturing and materials. Parts may be manufactured slightly too large or small, or the spacing between critical parts could differ. Similarly, parts may be slightly different colors or textures from what was specified.
My job as a product design engineer is to envision the ways that a part may not be manufactured correctly, and how that may impact the appearance and function of the final product. Rather than throw out parts that aren’t perfect, we use standards to define what’s acceptable. To deal with the variances in parts, we create tolerances, a golden sample, and limit samples, quantifying the allowable changes a part can have before it’s considered out of specification and rejected. Let’s dive into how setting these parameters can save the day.
Geometry tolerances
To define how different a part can be from the ideal shape, we use tolerances. Tolerances usually deal with changes to a part’s geometry: the size of a feature, the diameter of holes, or the flatness of surfaces. Engineers use statistical analysis, a deep understanding of manufacturing methods, and some witchcraft known as GD&T (geometric dimensioning and tolerancing) to determine and communicate these changes. We’ll save that for another article.
The golden sample and limit samples
In our CMF article, we review the common standards used to convey color, material, and finish of a manufactured part. These standards exist to ensure that a part made in China looks identical to a part made in America — and to ensure that designers, engineers, and factories all speak the same language. When we specify a color using a standard like Pantone, we’re actually using shorthand for an exact recipe of pigments to reproduce that color. Similarly, texture specifications ensure that two parts look and feel nearly identical regardless of when or where they’re manufactured.
Even with standard, parts will be manufactured that aren’t exactly the color or texture we specified. Painted parts tend to be very similar in appearance and texture. Plastic parts that are manufactured in the same batch also tend to be very similar. If you make a new batch of plastic parts, the color may vary slightly, as it needs to be dialed back in. Wooden parts tend to have the most variation because the wood grain and surface imperfections may stain or paint differently. To alleviate these issues, we create limit samples and golden samples.
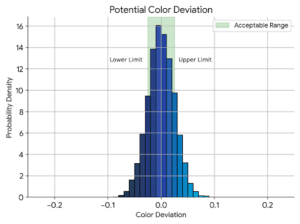
An example of how colors may deviate from the ideal (exaggerated to show differences). Anything outside of the acceptable range may be scrapped, which can be expensive! Find the balance between variation and cost.
A golden sample is the perfect version of the part. It’s the color, texture, and quality we strive for when we’re manufacturing parts. Limit samples help the factory understand how far away from the golden sample we’re willing to accept. This may be a part that’s too green, not enough green, too smooth, or too rough — but we still accept and use it. Anything beyond the parameters of these limit samples is rejected and scrapped. A well-defined set of limit samples allows for more parts to be accepted from the manufacturing line, reducing the costs to make the product. They also allow for the maximum amount of variation without compromising the quality of the product. We never want to place two units side by side and have obvious differences in their appearance.
To create limit samples, we tend to either use actual manufactured parts from trial production runs, or we intentionally make samples with variations in colors to set the limits. Quality-control technicians compare an assortment of manufactured parts against these limit and golden samples to ensure they fit within our tolerance range. Color sensors and controlled light boxes are used to ensure we eliminate additional variables like lighting, dust, or debris, or variations in how people see colors. Each product has unique challenges and requirements, so working with an experienced team helps to ensure you’re getting the best balance of cost and quality.
informal is a freelance collective for the most talented independent professionals in hardware and hardtech. Whether you’re looking for a single contractor, a full-time employee, or an entire team of professionals to work on everything from product development to go-to-market, informal has the perfect collection of people for the job.